Ceramic Anilox Roller
Ceramic Anilox Roller
The ceramic anilox roller adopts the plasma method to melt the thermal sprayed chromium oxide powder, melt spray coating on the surface of the metal smooth roller, and firmly combine with the metal roller to form a high-hardness and dense ceramic film, which is ground and polished, and then used The laser beam engraves ink holes on the ceramic surface, multi-beam high-precision laser engraving, regular mesh, smooth mesh, flat bottom, large amount of ink transfer, fast ink discharge, and easy cleaning.
The commonly used mesh types are quadrilateral, hexagonal, 45° oblique type, 60° oblique type, S type, etc. Different mesh types and mesh depths correspond to the application of ceramic anilox rollers in different fields.
- Base Material:45# steel, Aluminum alloy (or according to your needs)
- Surface Material: Al2O3, Cr2O3
- Surface Thickness: 0.25mm~0.3mm
- Surface Treatment:Thermal Spraying
- Surface hardness: HV 1250~1300
- Screen line: 30~1500LPI
- Max length: 4000mm
- Max diameter: 600mm

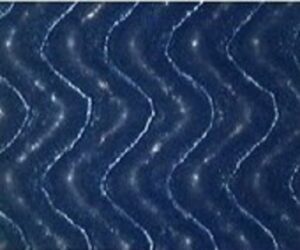
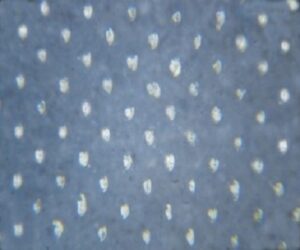
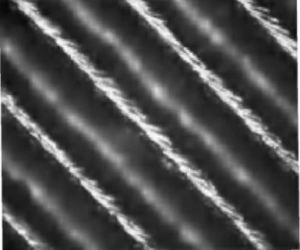
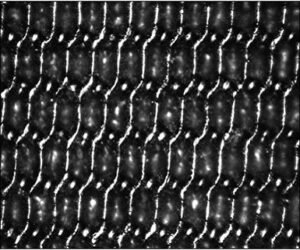
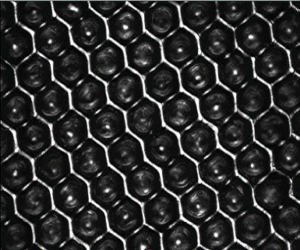
- Wear-resistant, corrosion-resistant
- The cell size is regular, the cell wall is smooth, and the cell bottom is flat
- Large amount of ink transfer, high precision
- The thickness of the surface ceramic layer is uniform, the degree of bonding is high, and the service life is long
- easy to clean
- All products provide factory quality inspection reports to ensure product quality and accuracy
Due to the excellent performance of ceramic anilox roller, it has been widely used.The main application fields of ceramic anilox roller are flexographic printing, gravure printing, coating industry, label printing,
carton printing, etc.
Flexo printing roller
Flexo printing is a printing method with a relatively high printing speed. Due to the high speed, it also has high requirements for the anilox roller used for ink transfer, and the anilox roller wears relatively fast under high-speed printing, which also There are high requirements for the wear resistance of the anilox roller. The ceramic anilox roller has the characteristics of strong ink adhesion, high hardness, good wear resistance and fast drying. It is a very cost-effective ink transfer roller in flexo printing.
Label printing roller
Label printing is currently the field with the highest precision requirements in flexographic printing. The ink transfer accuracy of the label printing roller is very high. Label printing generally uses UV ink, the printing temperature is generally low, and the ink viscosity is relatively high. If the quality of the roller surface is poor, the screen type selection is improper, and the ink is prone to fly ink after the scraper, which affects the overall printing effect. . If the number of label roll lines is relatively high, the mesh wall will be relatively thin, making the mesh wall brittle and prone to scratches under the action of the scraper, resulting in poor printing quality.
Carton printing roller
Carton printing is different from other printing methods, it belongs to sheet-fed printing. The substrate is corrugated cardboard, the surface of the substrate is relatively rough and has a certain thickness, and the printing accuracy of carton printing is not high compared to flexo printing, which is a kind of low-precision printing method. The carton printing roller needs to have the characteristics of durability and reliability, good transferability, and low cost of use to maximize the benefits of carton printing.
Offset printing roller
As one of the main printing methods, offset printing has the characteristics of high speed and high printing quality. Ceramic anilox rollers are also widely used in the offset printing industry.
The ink fountain roller, water fountain foller, and UV roller in the offset printing machine are all ceramic anilox rollers.
The ceramic anilox rollers form Herzpack are widely used in HEIDELBERG, ROLAND,KOMORI,MITSUBISHI,KBA and other machines.
Coating roller
Coating rollers are mainly used for anilox roll coating and sizing equipment. This coating equipment mainly uses anilox (concave) coating rolls for sizing coating. The coating is uniform and the coating amount is accurate. When coating with anilox roll, the coating amount is mainly related to the concave depth of the anilox roll and the type of glue. The deeper the concave depth of the anilox roller, the greater the amount of glue transferred from the concave holes to the substrate; on the contrary, the shallower the anilox roller mesh concave depth, the amount transferred to the substrate is correspondingly reduced.
Micro gravure roller
Micro gravure roll, the so-called micro means that the diameter of the anilox roll is smaller than that of the traditional anilox roll. The diameter of traditional anilox rolls, which are widely used today, is usually 125 to 250 mm. The diameter of the gravure roll is usually only 20 to 50 mm, and the slightly larger is 50 to 100 mm. The smaller the diameter of the roller, the smaller the contact line between the substrate and the roller. When the contact line is smaller, the possibility of coating defects is less.
CONTACT US
Connect
Phone: +86-21-60674601
Mobile: +86 13918369684
Whatsapp:+86 13918369684
Fax: +86-21-60674601
Email: Abel@herzpack.com